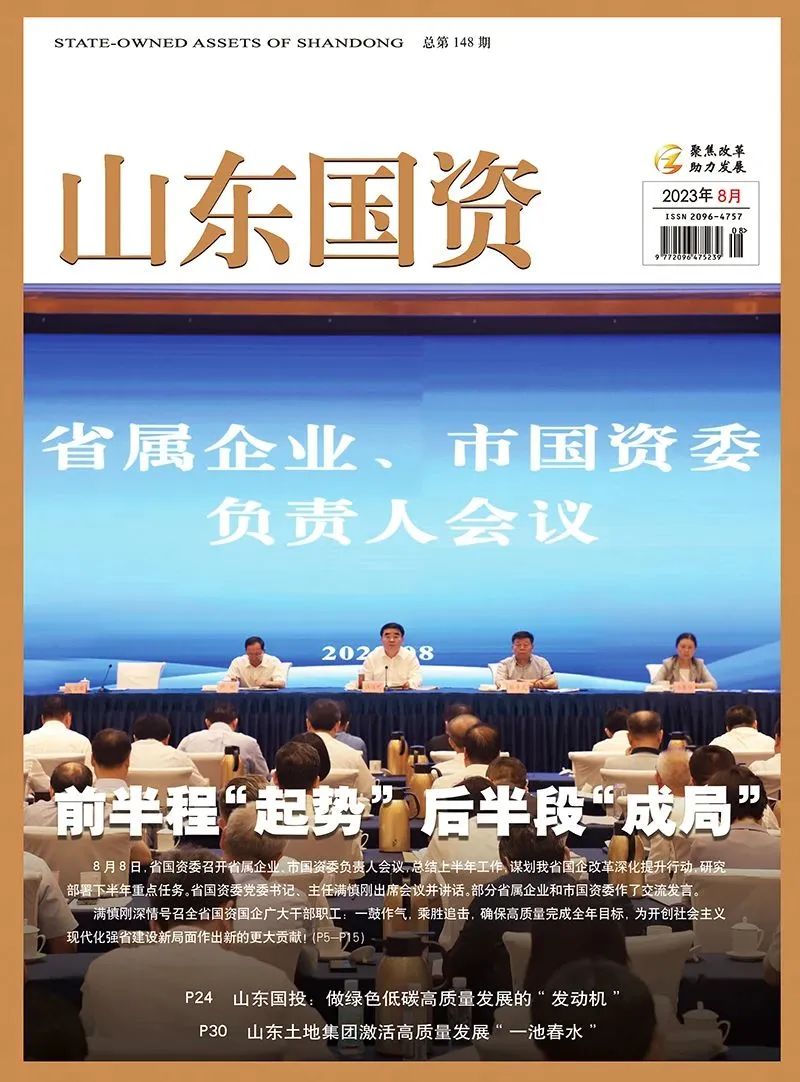
今年以来,东华重工轻合金公司持续巩固深化“两化融合”管理成果,坚持“融合重塑、创新实干”理念,以市场机制撬动提质增效,以精益运营助推管理升级,深入推行市场化精益化“六精六提”融合管理,为公司高质量发展提供有力支撑。
(宋姣根据生产信息系统反馈数据,检查工作进度完成情况)
宋姣是轻合金公司挤压一车间运行二班班长,他所在的班组,涉及挤压、牵引、矫直、锯切、精整、时效包装等多个工序,职工分布在长达近300米生产线上。
(宋姣扫码获取当班职工工作量)
轻合金公司把解决生产运行实际困难作为精益化管理主攻方向,深度开发运用生产管理系统,构建以挤压、熔铸系统团体作业结算为主,模具、质控系统个人作业结算为辅的信息化结算体系,围绕主要生产工序,修订完善内部结算价格312项,实现三、四级市场“工作扫码、数据归集、人员匹配”无纸化结算。搭建内部检修、内部检测、离线淬火、车皮镗孔等结算线上审批运行模块,消除时间浪费,提高生产效率,降低管理成本。
“我们妥善应对新形势、新变化,采取生产自动化、管理信息化、数据可视化等智能化手段,加快数字化转型升级步伐,进一步提高市场化精益化管理水平。”轻合金公司副总经理张新峰介绍道。
“根”上分析,让管理长出“前后眼”
办法总比困难多,源头治理是关键。
长期以来,该公司挤压生产工序受型材风冷水冷工艺、型材断面结构、形位尺寸等要求制约,造成待精整型材种类多、难度大,对订单交付产生一定影响。
(精整攻关小组带头人李刚正在检验型材尺寸)
他们成立攻关小组,认真分析问题存在原因、确定改善指标、厘清改善措施,制定挤压作业标准12项,明确调水、调风、垫石墨、矫直的作业标准,减少型材形变,降低精整难度,其中针对水冷挤压产品,优化挤压作业参数,制定首料牵引及淬火水量参数标准,保证型材水冷变形后整体可控。先后建立疑难断面精整作业标准22项,实施精整设备维修改造20项,设计扭拧矫直、撑腔、扭拧整形等精整专用工装15件,型材精整率降低5%。他们将12个典型案例操作流程进行归纳汇总,分类制作PPT,形成可借鉴、长期性的作业指南。
“台”上分享,将精益理念“传播开”
(轻合金公司自主改善暨员工创新工作法分享会现场)
(模具车间青工张龙正在向工友分享创新创效经历)
“通过自主改善案例分享会,让一线职工上讲台,分享自主改善心得,更能推动精益思想及工具方法的渗透。”“六精六提”办公室负责人李慧燕说,他们巧用钉钉系统,建立线上“提报、初评、复评”工作模式,自主改善项目由提报任务的职工完成,公司组织“评审团”给出评价,视改善提升的价值给与职工奖励,这种方式让一线职工更多关注岗位上的问题、想办法解决问题,而且收入也提高了。
今年以来,他们共收集自主改善项目452项,评出公司级优秀案例398项,奖励400余人次,发放奖励4万余元。在为公司创效的同时,自己还能多挣一份钱,目前自主改善行为在职工思想中已形成共识,大家都在朝着“多、快、好、省”的目标前进。